The Construction Method and Advantages of Prefabricated Houses
Prefabricated houses are the homes of the future. The construction time for a prefabricated house is very short. From the signing of the construction contract to moving in, it typically takes about two months. When the construction team arrives at the site, the house framework is usually completed in one day, including the roof. Unlike traditional construction, drying time is not required. The quick construction time saves you money.
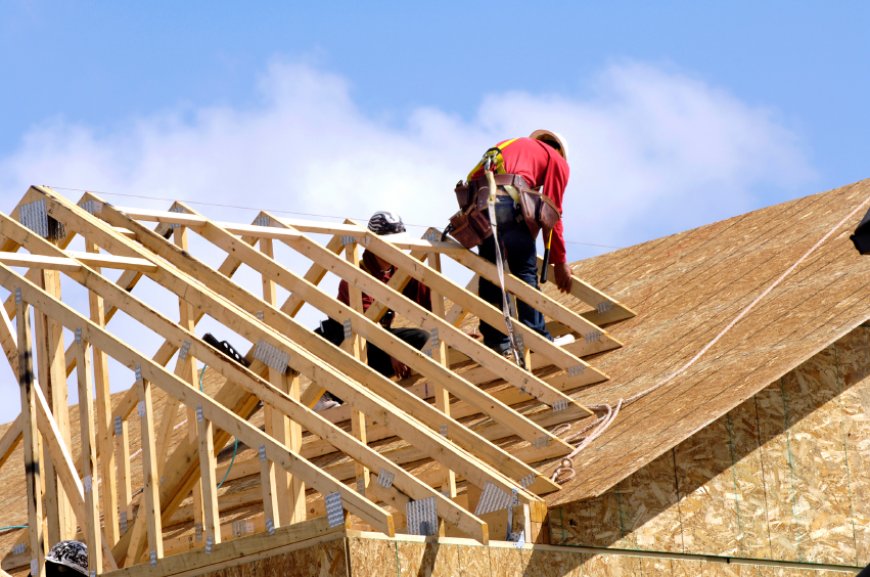
The construction time of a prefabricated house is very short. From signing the construction contract to moving in, it typically takes about two months. Once on-site, the construction of the house framework is usually completed in one day, including the roof. Unlike traditional building methods, no drying time is required. The fast construction time saves you money.
CONSTRUCTION METHODS AND MATERIALS
Construction Works
After marking the building's location, the site is cleared, and a 15 cm layer of humus is excavated. Then, trenches are dug for the foundation strips. The foundation strips are set at a depth of 80 cm below the ground level and are made of compacted concrete (MB15), 35 cm thick. Beneath them, a 10 cm layer of compacted gravel is placed as a cushion.
The plinth walls are constructed on top of the foundation strips using compacted concrete (MB20) in a double formwork and are finished with reinforced concrete ring beams. The wall thickness is 25 cm, and the height is 45 cm above the sidewalk level. Between the plinth walls, soil is filled and compacted in layers to the required density and height.
On top of the compacted soil between the plinth walls, a 10 cm thick gravel cushion is placed, which serves as a base for the concrete floor slab. The floor slab is made of compacted concrete (MB20), 10 cm thick.
Waterproofing is applied over the plinth walls and the floor slabs in two stages. In the first stage (before assembling the building), waterproofing strips 50 cm wide are applied. In the second stage (after the building is assembled), the remaining surface is covered with waterproofing.
WALL ELEMENTS AND STRUCTURES
Wall elements are fabricated in the workshop according to the project specifications and delivered to the construction site. The elements are produced in modular dimensions of 120x260 cm and 60x260 cm and can be either external or internal, solid or with pre-installed windows and doors, depending on their position within the building.
The construction of external elements consists of a wooden frame (100 mm thick), while internal elements use a frame of 80 mm thickness. Both sides of the frame are covered with 10 mm thick OSB panels. Between the panels, external elements contain compressed mineral wool (100 mm thick) and PVC foil, while internal elements use compressed mineral wool (80 mm thick).
After assembling the building, the exterior walls are covered with "Izoterm" cladding (100 mm thick), while the interior walls are finished with 12.5 mm thick gypsum board. Elements for bathrooms and kitchen areas are covered with waterproof gypsum board (12.5 mm thick). Along with the final interior cladding, joint fillers and tape for seam treatment are supplied.
The cladding is secured using appropriate fasteners or nails. The assembly of the elements and their connection into a unified structure is done using wooden foundation beams, corner joints, and trims, which are inserted into pre-made grooves. The foundation beams are coated with bitumen and anchored to the plinth walls. During the fabrication of the elements, flexible plastic pipes are installed for electrical distribution wiring.
JOINERY
The exterior joinery is made of six-chamber PVC profiles with appropriate hardware. The selection and sizing of openings are done according to the requirements of the room in which they will be installed, in full accordance with the project.
Windows and doors are installed in the wall elements on-site after assembly and roofing are completed.
Interior single-leaf doors are made of double-plywood, either solid or glazed.
The entrance door is secured with a security lock – with a cylinder, while other doors are fitted with standard locks.
ROOF STRUCTURE
The roof structure is made of truss roof supports with a 25° pitch. The trusses are constructed from air-dried spruce wood of class I/II, all according to static calculations. The trusses are mounted on the wall structure at modular distances and anchored using appropriate metal profiles. The trusses are interconnected with 24 mm thick wooden sheathing in the roof planes, ceiling battens in the ceiling planes, and vertical braces, ensuring the spatial stability of both the roof and the building.
On top of the wooden sheathing, a layer of roofing paper is applied, followed by longitudinal and transverse battens (24/48 mm) to allow ventilation beneath the roof covering. The roof is covered with interlocking tiles (falcovan tiles). The ridge parts of the roof are clad with 10 mm thick OSB panels and "Izoterm" insulation (100 mm thick).
The eaves of the roof are finished with planed spruce boards (20 mm thick), while the roof edges are covered with aluminum soffit, mounted over battens (40/48 mm).
CEILING CONSTRUCTION
The ceiling construction consists of a grid, insulation, vapor barrier, and ceiling cladding. Below the lower straps of the roof trusses, a grid made of battens (48/40 mm cross-section) is installed. Over the grid, a vapor barrier made of PVC foil is placed, followed by a ceiling cladding of 12.5 mm thick gypsum boards.
On top of the grid and ceiling cladding, between the straps of the roof trusses, thermal insulation made of compressed mineral wool (150 mm thick) is installed. The grid and ceiling cladding are secured with appropriate nails. Along with the ceiling cladding, filler and joint treatment tapes are provided.
OTHER ELEMENTS
All columns, floor beams, and railings are made from high-quality, planed spruce timber, in full accordance with the project.
CRAFTSMANSHIP WORKS
Windows are glazed with low-emission glass, with a composition of 4+16+4 mm.
INTERIOR FINISHING
The ceilings are painted with white semi-dispersion paint, following the necessary preparation of the gypsum board joints, including filling, bandaging tape, and joint compound.
The finishing of interior walls is done with semi-dispersion paints, with the required preparatory work performed, similar to the ceiling treatment. The basement ceilings and walls are also finished with semi-dispersion paint, with the appropriate preparatory steps.
All joinery is painted with Sadolin wood finish. The treatment of all interior surfaces is done in two coats.
The choice of tones for finishing all surfaces is made by the supervising authority or the project designer before the materials are delivered to the construction site.
The bathroom walls are covered with ceramic tiles (locally produced) up to the ceiling, while in the kitchen, they are tiled up to a height of 160 cm from the floor level.
EXTERIOR FINISHING
The finishing of exterior surfaces made of Izoterm is done with a plastic, rough-textured plaster, while the exterior woodwork is painted with Sadolin wood finish. The plinth walls are painted with facade paint.
INSTALLATION WORKS
The project includes plumbing and sewage installations, as well as electrical installations, which are detailed in the specific sections of the main project.